Variable Speed Drives
A variable speed drive (VSD), sometimes also called Variable Frequency Drive (VFD), frequency inverter, AC drive, is an electronic device that allows operators to change the speed at which an AC motors runs. Variable speed drive receives AC power and converts it to a variable frequency, variable voltage output for controlling AC motor operation. A typical variable speed drive receives 380V AC, three phase, 50 Hz input power and in turn provides the proper voltage and frequency for a given speed to the motor.
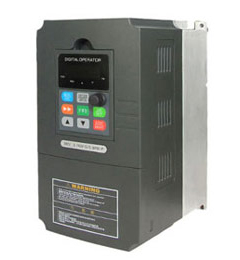
The combination of a variable speed drive with a motor is becoming increasingly popular as a final control element because it consumes less power than a motor running at full speed and a control valve. Indeed, the China Energy Association is encouraging the use of variable speed drive for AC motor speed control to reduce power consumption. However, obtaining good control depends upon proper selection and installation of the variable speed drive as well as understanding how control may differ with a variable speed drive.
In this time some power factor corrections are included active filters, so in some cases we do not need to have harmonic filter for each equipment. Active filters analyze the harmonics drawn by the load and then inject the same harmonic current to the load with the appropriate phase. As a result, the harmonic currents are totally neutralized at the point considered. This means they no longer flow upstream and are no longer supplied by the source. A main advantage of active conditioners is that they continue to guarantee efficient harmonic compensation even when changes are made to the installation.
In design stage can calculate how much harmonic can reduce by this device, and which one needs independent harmonic filter, especially in high number of variable speed drive in service.
There are twice as many power components in an AC drive as in a DC drive. In the past, the regulator has been approximately twice as complex as that of a DC drive. Present with digital technology or state-of-the-art electronics allows this factor of complexity to come much closer to 1:1 than 2:1. Circuits that were difficult to produce with discrete parts can now be accomplished with large scale chips and microprocessors. This has greatly reduced the complexity differences between AC drives and DC drives.
In summary, conversion of DC to AC is possible but hard to achieve if you can not have your manufacturer or drive supplier provide you already with some similar or identical application. You need to get the answer from him but the project has to be a viable option (cost) for you also! The conversion will be very expensive compare to staying with DC (existing or brushless). However, if you can improve your production, process etc... in the long run, it will be a good choice.
There are also different types of variable speed drives for different types of motors, that is synchronous or induction for example. Therefore, evaluating case by case makes sense and other considerations along with the above mentioned also needs to be carried out. Here are some examples.
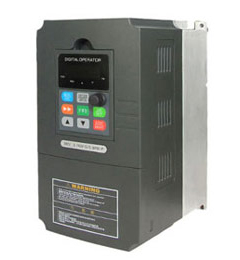
- There are multiple motors that must start with the variable speed drive to reduce the starting current. In this case, one should consider the number of motors that can start in succession, using the same variable speed drive.
- Check with the variable speed drive manufacturer whether they offer a simplified variable speed drive for starting only. For starting only, the losses aren't of greater importance. Preferably you may want the variable speed drive to come with bypass switch already incorporated to it.
- As it comes to low cost soft starters, those vary only voltage, never forget that these soft starters reduce the torque of the motor to the ratio of voltage to the power of 2.2 (yes 2.2, not 2), so you will want to evaluate if the motor will accelerate the load with the desired voltage, and if so, without overheating. Also remember that some loads are more demanding than others. Check for torque requirements and load inertia. If the motor can accelerate, then a soft start can be used. If not, a variable speed drive can be one solution.
- When the process requires, or the output of production varies, the application of a variable speed drive makes sense.
The most critical selection factor: working current. Actually, choose the VSD according to the working current is the final step in the entire selection process. Here is to emphasize. Sizing the variable speed drive according to the motor actual operating current (not the nameplate current) rather than the nameplate power.
Basic principle, while working in a long time: variable speed drive output current > Motor current
Other factors for selecting variable speed drive
- Altitude.
- Ambient temperature, transport and storage temperature, enclosure.
- Input line voltage level, frequency, variable speed drive output frequency range.
- The variable speed drive efficiency, overload capacity, cooling methods.
- Size, structure, installation way.
- etc...